Weber 121 Wrap-Around Label Applicator
Weber’s versatile 121 provides a simple, cost-effective solution to low-volume wrap-around labelling that is as accurate and flexible as similar labelling systems used in larger-scale operations. This labelling system features the fast and accurate positioning of full, overlap and partial-wraps of pressure-sensitive labels on cylindrical containers.
Products up to 7″ in diameter and up to 12″ high easily can be accommodated using the system’s adjustable guide rails. It can handle labels up to 6 inches tall and 12 inches long and apply them at rates up to 45 products per minute to a variety of sized products. During application, labels are peeled away from the liner and securely attached to products using the wipe-on label applicator and a wrap station.
The brand-new Weber 121 system features a cost-efficient Alpha Compact labelling system mated with a wrap conveyor for a compact, easy-to-use solution for labelling bottles and other round straight-walled products. This heavy-duty wrap-labeller can be inserted into your production line to give you consistent end-to-end labelling and better control over your production.
Applies label up to 6″ high x 12″ long
Stand-alone or add to a production line
Placement accuracy of 0.03″
If you are looking for a reliable, economical bottle-wrap labelling system that is easy to set up and simple to maintain then check out the Weber 121. Industries that use the Model 121:
Craft beer labelling
Medical and pharmaceutical container labelling
Food/Sauce bottle labelling
Cylindrical beverage & juice bottle labelling
Products are delivered to the Weber 121’s built-in Alpha Compact applicator head via a 7.75″-wide, 45″-long belt conveyor, which permits product transfers at both the entry and discharge ends. The unit is capable of a superb placement accuracy of 0.03″. The Weber 121 can be integrated into existing production processes or operate as a manually fed, stand-alone solution. The unit also boasts robust steel construction that makes it ideal for lower-volume, intermittent labelling projects or for multiple-shift operations.
Adobe Reader is required to open and view PDF files. This can be downloaded free from adobe.com.
Available Documents
Geset 121 Instructions ManualGeset 121 Computer Assisted Design
Geset 125 Horizontal Labelling System
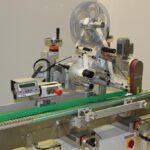
The Geset 125 labelling system is used to label cylindrical products automatically. Depending on the type and dimension of the product, different label sizes are used. The products are fed manually or by a conveying system provided by the customer at an infeed passage of the labelling system. Care should be taken on accurate alignment of the products between the two freely mounted rollers of the roll conveyor. The side guide’s position the products flush with the outside edge of the roll conveyor.
The roll conveyor feeds the products to the labeller. There the label is applied with the part running forward onto the product and it is pushed by rotation and the back pressure of the wrapping unit onto the product. The back pressure of the wrapping unit (the speed of the wrapping unit is twice as fast as the speed of the base conveyor) enables the product in rotation. The roll conveyor forwards the finished labelled products to the outfeed. Here the products are removed manually or by the customer’s conveying system.
View ProductECOMARK – Economical Wax
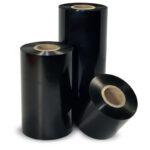
ECOMARK is the most competitive wax ribbon from Weber.
It makes no compromise between price and quality in order to match
standard wax labeling applications.
Markoprint IP-Jet
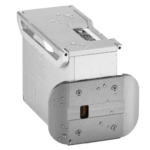
The thermal inkjet printer IP-JET HP MK3 has been specifically designed for usage in dusty or damp situations. It is especially ideal for the food sector, as well as the plastics, pharmaceutical, and chemical industries, due to its IP65 protection level.
The IP-JET HP is a small inkjet printer with a printhead and control unit housed in one unit. Water and dust are kept out of the cartridge by sealing it and pressurizing it. The power supply features a waterproof connector, and the external connections’ connectors are secured with an IP67 rating. The printhead does not need to be covered or removed for wet cleaning, unlike many other printers on the market.
View ProductZebra FS20 Fixed Industrial Scanner
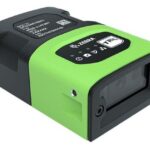
An Easily Integratable Scanning Solution
The increasing demands of international commerce and its global supply chain are pressuring companies to deliver more — and to do it faster. From manufacturing to logistics to the end customer, success is driven by the ability to quickly move and track the products that drive your business.
Address it all with the compact Zebra FS20 Fixed Industrial Scanner. With the FS20, it’s easy to track and trace every item as it moves through production, storage and fulfilment. Scan barcodes on components moving through your assembly line to ensure the right part is used at the right time — and enable rapid targeted recalls of products that contain defective parts. Scan barcodes on items as they are placed on warehouse shelves to provide visibility into real time inventory. And scan barcodes when fulfilling orders to ensure the right items are sent to the right customer. Whatever you want to track and trace, the FS20 makes it easy.
View Product