DS3608-DP/DS3678-DP 1D/2D
Unstoppable Performance for 1D/2D Direct Part Marks (DPM) and Bar Codes
As a member of the Zebra 3600 Ultra-Rugged Series of scanners, the practically indestructible 1D/2D DS3608-DP corded and DS3678-DP cordless scanner brings the dependable lightning-fast capture of virtually every direct part mark to aerospace, automotive and other manufacturing plants where end-to-end traceability of every product component is required.
Innovative Features of the DS3608-DP/DS3678-DP 1D/2D Ultra-Rugged Scanner
Superior performance
When it comes to capturing barcodes in the manufacturing plant, the DS3608-DP and DS3678-DP deliver the ultimate in scanning performance—period. Capture direct part marks regardless of size, surface, contrast, density or type—including challenging dot peen, chemical or laser etch, ink, inkjet mold, cast or thermal spray marks. And workers can capture any 1D or 2D barcode displayed on a screen or printed on a label in practically any condition for superior barcode capture flexibility in a single scanner.
Ultra-rugged design
The manufacturing plant floor is as tough as its gets—and the cost of unplanned downtime on the production line is astronomical. That’s why we created a new product category—the ultra-rugged scanner. This dust-tight and waterproof scanner offers the highest drop, tumble and sealing specification in this class, and is the only scanner to offer two sealing ratings—IP65 and IP67.
Unrivalled manageability
With our complimentary industry-best tools, managing these scanners couldn’t be easier. Users can remotely configure and upgrade scanners, format data properly for instant transmission into business applications, monitor battery statistics for cordless models and more.
Unbeatable features
In addition to superior scanning performance, flexible information capture, an ultra-rugged design and unparalleled manageability, workers get more features that help these scanners capture every high density bar code on the first try. Whether direct part marks are very low contrast or printed on shiny, reflective surfaces, the DS3608-DP and DS3678-DP do it all.
Adobe Reader is required to open and view PDF files. This can be downloaded free from adobe.com.
Available Documents
DS3608Markoprint Integra Ultimate
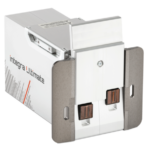
The innovative Integra Ultimate thermal inkjet printer not only provides IP65 protection against dust and moisture, but it also closes and cleans the nozzle plate at each pause. This system ensures that the printing is always clean, with faultless results even after extended breaks. As a result, the ink cartridges’ open times are multiplied many times. Two HP Class thermal inkjet ink cartridges can be used with the print head. As a result, the system produces beautiful prints with a maximum height of 25 mm.
View ProductULTRAPRINT – High durability resin
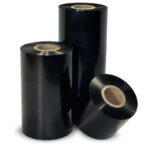
ULTRAPLATE is the standard resin ribbon from Weber. It is dedicated to
applications requiring a perfect printing quality and excellent mechanical
resistances. Its high versatility (it also prints on coated papers) and its
performances (sharpness, printing speed) have resulted in making
ULTRAPLATE a market reference.
Markoprint Integra PP RAZR
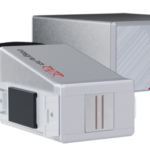
Experience Effortless High-Resolution Printing: Introducing the Integra PP RAZR with Cutting-Edge Technology. Print Up to 34mm High on Virtually Any Product Surface with Ease. Be Amazed by the Permanent Print Head’s Impressive Resolution, Lightning-Fast Speed, and Integrated Redundancy. Plus, its Compact Design Ensures Seamless Placement in Any Production Facility.
View ProductMarkoprint NonStop Printing
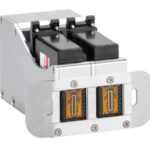
To enable continuous marking in ongoing production, our Markoprint NonStopPrinting printhead holds two alternately printing cartridges. Because the other ink cartridge is printing on the same position, each ink cartridge can be changed, cleaned, or serviced without pausing the machine.
An intelligent automatism prevents both cartridges from going empty at the same time. The first cartridge will always print two consecutive print jobs, taking turns with the second cartridge, which will only print one. This sophisticated automatism avoids both cartridges from running out at the same time. This will keep the ink from drying out in both cartridges. When the cartridge with the larger print volumes is empty, a warning will show, and the other cartridge will continue printing until it is replaced. The new cartridge will print the lower quantities to allow for you to replace the “older” cartridge. A sophisticated workflow that will boost your efficiency and productivity.
View Product