Weber Alpha Compact Applicator
The new Alpha Compact label dispenser now sports a new design with increased performance and higher application rates and is even simpler to operate than its tested and proven predecessors. As always, this system applies quickly and accurately pre-printed labels onto products and packaging in conjunction with various applicator units. The newly integrated controller now renders the…
The new Alpha Compact label dispenser now sports a new design with increased performance and higher application rates and is even
simpler to operate than its tested and proven predecessors. As always, this system applies quickly and accurately pre-printed labels onto products and packaging in conjunction with various applicator units.
The newly integrated controller now renders the Alpha Compact particularly space-saving and optimal to operate. Using a conventional PC with USB interface, different labeling parameters as well as functions like start and stop, single label feed, speed control and sensor calibration can now be entered and stored in the Alpha Compact.
Data and information backup and convenient transfer of dispenser parameters to other Alpha Compact systems is truly simple now. The changeover of labeling orders in conjunction with system controller can now become automatic.
Unsupported connections to existing system controllers are also possible and provided. Stored parameters and jobs can be called up from extensive internal data storage and can also be edited and used for different labeling jobs. A second miniature controller enables 1:1 labeling and simulates the well-known Alpha series (2 rotary and 4 push buttons) input unit, proven a thousand times over.
Adobe Reader is required to open and view PDF files. This can be downloaded free from adobe.com.
Available Documents
Printer_Applicator_Solutionsweber-alpha-compact-product-sheet
Markoprint Integra One ip LX
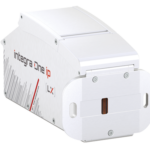
Unleash the Power of Proven Washdown Technology (IP Protection) for Seamless Performance in Complex and Demanding Applications. Experience High-Speed Printing and Effortless Operation with Up to 10 mm Print Distance. Discover Impressive Innovations, including a Patented Mechanism for Secure Ink/Printhead Unit Hold, Setting a New Standard in Printing Excellence.
View ProductZebra FS70 Fixed Industrial Scanner
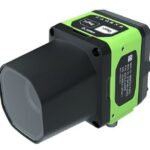
Today more than ever, the increasing demands of international commerce and its global supply chain are pressuring companies to deliver more — and to do it faster. From manufacturing to logistics to the end customer, success is driven by the ability to quickly move and track the products that drive your business.
The FS70 Fixed Industrial Scanner is your configurable and customisable solution. Easily keep pace with your business, enabling quality control and track-and-trace of every part and package as it moves through production, storage and fulfilment. Whether you need a high-powered lens to read a very small barcode from a long distance, or a wide-angle lens to capture barcodes on extremely large parts, the FS70 addresses it all. C-mount external lenses allow you to achieve the working range and field of view your application and environment requires. And compatibility with virtually any external lighting solution ensures reading of the most challenging barcodes — even low-contrast direct part marks or those printed on curved or reflective surfaces. The result? Best-in-class production, warehousing, distribution and logistics processes that inspire your business to reach its highest potential.
View Product
Zebra FS10 Fixed Industrial Scanner
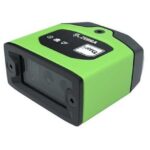
A Quick & Compact Scanning Solution
The increasing demands on international commerce and its global supply chain are pressurising businesses to deliver more and deliver faster. From manufacturing to logistics to the end customer, success is driven by the ability to move quickly and track the products that drive your business.
Now you can address it all with the compact Zebra FS10 Fixed Industrial Scanner. With a slim profile, the FS10 fits easily everywhere you need scanning. Just plug the FS10 into the USB port of a workstation, laptop, tablet or any other host device to dependably capture barcode data, from assembly to storage and fulfilment.
View ProductMarkoprint Integra PP 108
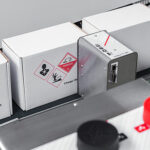
The Markoprint Integra PP108 is the first inkjet printer with SEIKO printing technology and a circulating ink system. It features a POZIFLOW circulating ink system which prevents the accumulation of air in the nozzles and ensures a permanent, clean print image without missing print due to blocked nozzles. The system’s ink tank can be installed above, below, or at the same height as the print head without any problems. The new SEIKO printhead has a print height of 108 mm and achieves a remarkable speed of up to 150 meters per minute with a high resolution of 360 dpi.
Suited to Dual Colour Printing Applications such as Hazard Labelling, Dual Colour overprinting and Direct Printing Applications to corrugate, and web printing applications, the PP108 is the latest high end, economical Inkjet System using the latest Drop on Demand Printing Technology.
View Product