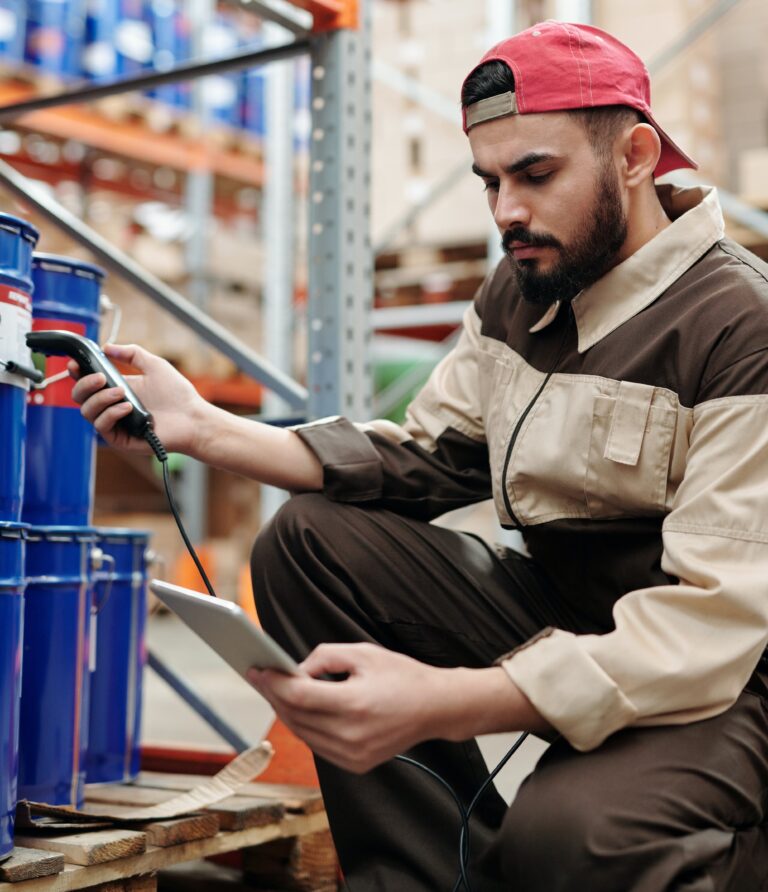
Introduction
Label quality inspection is an essential step in the label manufacturing process, ensuring that labels are of high quality and free from defects. It is crucial that label manufacturers comply with quality inspection standards to protect consumer health and safety. As technology continues to advance, innovations in label quality inspection technology are improving quality inspection accuracy, efficiency, and reliability. In this blog post, we will explore the importance of label quality inspection in the manufacturing process and discuss some of the latest innovations in label quality inspection technology, including vision systems, artificial intelligence, barcode verification systems, and automation. We will also examine how these innovations are changing the label manufacturing industry and what we can expect to see in the future.
Importance of Label Inspection in the Pharmaceutical, Food, and Medical Industries
Labelling is a critical aspect of the pharmaceutical, food, and medical industries. These labels provide important health and safety information to consumers, ensuring that they can make informed decisions about the products they use. However, when labelling errors occur, the consequences can be severe.
In the pharmaceutical industry, for example, labelling errors can lead to confusion, incorrect dosages, or the use of the wrong medication altogether. This can have serious consequences for patient health and can even be life-threatening. In the food industry, labelling errors can lead to allergic reactions or other health issues for consumers.
To prevent these kinds of errors, strict regulations for labelling exist in these industries. These regulations require manufacturers to include specific information on labels, such as dosage instructions, allergen warnings, and product expiration dates. Labels must also be clear, legible, and free from defects that could lead to confusion.
However, simply complying with regulations is not enough. Label manufacturers must also take great care in their quality inspection processes to ensure that the final product meets both regulatory requirements a
nd customer specifications. This requires a thorough understanding of the materials and printing processes involved in label manufacturing, as well as the potential defects that can occur.
One of the most important aspects of label quality inspection is ensuring that the label is free from defects that could lead to confusion or harm. This can include smudges, missing text, filled-in print, incorrect colours, non-scannable barcodes, and off-registration. Any of these defects can lead to confusion or even harm to consumers, which is why manufacturers must take great care in their inspection processes.
In addition to preventing harm to consumers, effective label quality inspection can also help manufacturers avoid costly product recalls and reputational damage. By investing in high-quality inspection equipment and processes, manufacturers can ensure that their labels meet the highest standards of quality and compliance.
Methods of Label Inspection in the Label Manufacturing Process
There are several methods of label qual
ity inspection inspection that manufacturers can use to detect defects and ensure the highest quality.
One of the most traditional methods of label quality inspection is using the human eye. This method involves visually inspecting each label for defects such as smudges, missing text, or off-registration. To ensure accuracy, manufacturers often use a strobe light to flash the label, making it appear as a frozen image rather than a speeding one. While this method can be effective for many types of labels, it is not ideal for medical labels, where the risk of human error is too high.
To minimize the risk of human error, Weber are investing in automated inspection equipment. These systems use high-resolution cameras and software to identify defects that may not be visible to the human eye, such as minute variations in print quality or colour accuracy. By automating the quality inspection process, manufacturers can reduce the risk of errors and ensure a higher level of accuracy and consistency.
There are several types of automated inspection equipment that manufacturers can use, depending on their specific needs. One common type is the vision system, which uses cameras and
software to inspect labels for defects. These systems can be set up to inspect labels as they move along the press, providing real-time feedback on quality and identifying defects before they make it to the customer.
Another type of automated quality inspection equipment is the barcode verifier, which is used to ensure that barcodes are readable and scannable. Barcodes are a critical component of many labels, providing important information about the product and enabling efficient inventory management. However, if a barcode is not scannable, it can cause confusion or delays in the supply chain. Barcode verifiers use specialized software and hardware to ensure that barcodes are accurate and can be read by scanners.
In addition to automated quality inspection equipment, some manufacturers are also using machine learning algorithms to analyse label data and detect patterns in defects. By identifying common types of defects and their root causes, manufacturers can take steps to prevent these issues from occurring in the future.
Importance of Label Quality Inspection in Ensuring Consumer Safety
For pharmaceutical products, labels must provide accurate information about dosage, administration, and potential side effects. Any mistakes or inaccuracies in this information can lead to serious health consequences for the patient. For example, an incorrect dosage or administration instructions can result in a patient receiving too much or too little of a medication, leading to adverse reactions or ineffective treatment.
Similarly, in the food industry, labels must accurately list all ingredients and potential allergens to protect consumers with food sensitivities or allergies. Any omissions o
r inaccuracies in this information can lead to serious health consequences for the consumer. For example, a consumer with a peanut allergy may suffer a severe reaction if peanuts are not listed as an ingredient in a food product.
In the medical industry, labels must provide accurate information about the use and application of medical devices. Any mistakes or inaccuracies in this information can lead to serious harm or even death for the patient. For example, a medical device used to monitor a patient’s vital signs may fail to operate correctly if the label instructions for use are incorrect or unclear.
To ensure consumer safety, label manufacturers must take great care in their quality inspection processes. The quality inspection process starts with the quoting and proof process, where the label manufacturer must ensure that the product matches the specifications requested on the proof. This includes checking the material used, making sure the barcodes are readable, and ensuring that the text is clear. If the job requires 100% inspection, each label is inspected for print quality.
Manufacturers can use a variety of methods to inspect labels, including using the human eye, vision systems, barcode verifiers, and machine learning algorithms. By investing in advanced quality inspection equipment and methods, manufacturers can ensure that their labels are of the highest quality and free from defects. This not only helps protect consumers but also helps build trust between manufacturers and their customers.
How they Work?
Label defects can be a nightmare for label manufacturers, causing confusion and harm to consumers, as well as financial losses. That’s why it’s crucial to inspect labels for defects before sending them to customers. In the label manufacturing process, quality inspection is critical to ensure that the final product meets regulatory requirements and customer specifications.
Weber has made improved quality inspection quality a top priority. To this end, Weber has chosen video inspection systems from Advanced Vision Technology (AVT). The new vision systems will provide 100 percent inspection at line speeds, a level that cannot be achieved with traditional manual methods or sampling plans.
By identifying and fixing any problems as they occur, Weber will be able to reduce both scrap and cost, making it a green manufacturing solution. Ultimately, Weber and its customers will benefit from higher productivity and reduced waste. The first two units will be installed soon, and the other four will follow over the summer. Weber will post pictures and videos of the units after they’re set up. With these advanced inspection systems, Weber can ensure that its labels are of the highest quality and free from defects, building trust between the company and its customers. Find out more by contacting one of our representatives today.