HP (Hewlett-Packard)
Hewlett Packard is a printhead suitable for marking almost any product at high resolution.
Click on the Direct Sales Button, and contact us today to order your HP inkjet thermal inks.
- very high reliability and safety under operational conditions
the cartridge and the complete printhead are exchanged simultaneously.
This guarantees consistent typeface quality.
- high printing speeds in barcode quality
up to 180 m/minute at 300 dpi resolution (maximum 300 m/minute)
- brilliant print image
with ink cartridges (thermo inkjet) of consistent quality, up to 600 dpi resolution (at 45 m/minute), achieved by ejecting tiny, accurately placed droplets from hundreds of minute nozzles at very high frequency.
- maintenance-free and simple operation
with patented Click´n Print cartridge replacement system. Cartridge installation is clean and simple. - high flexibility
by deploying several HP printheads. Print heights of maximum 12.5 mm to 100 mm are possible, and layouts are freely configurable. Multi-sided coding of packaging on two sides (top, side or at different production lines). Virtually all porous and non-porous surfaces can be marked, depending on ink type. Distance of printhead to product surface ranging from 0.5 to 5 mm. - highly economical
low operating costs but also high availability through simple and clean ink exchange, zero maintenance, immediate write response and uninterrupted operation. - simple installation
by dint of very compact design, with 3 different printhead types available
Adobe Reader is required to open and view PDF files. This can be downloaded free from adobe.com.
Available Documents
Markoprint Integra Ultimate
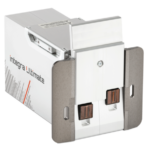
The innovative Integra Ultimate thermal inkjet printer not only provides IP65 protection against dust and moisture, but it also closes and cleans the nozzle plate at each pause. This system ensures that the printing is always clean, with faultless results even after extended breaks. As a result, the ink cartridges’ open times are multiplied many times. Two HP Class thermal inkjet ink cartridges can be used with the print head. As a result, the system produces beautiful prints with a maximum height of 25 mm.
View ProductDURAPRINT – Wax resin
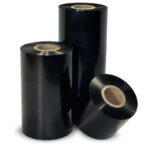
DURAPRINT is a very versatile, multi-purpose wax-resin ribbon.
It provides a higher level of resistances compared to standard wax ribbons and
prints small characters and barcodes with a high level of quality.
Markoprint Shutter Printhead HP
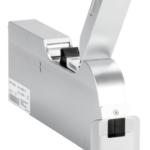
Inkjet nozzles can clog and dry up in a dusty printing environment, which is typical in wood-processing enterprises and other sectors. This results in poorly printed images. Our Markoprint Shutter Printhead HP prevents dust from entering the ink cartridge or gathering on the nozzles. During a production halt, the printhead automatically retracts the cartridge and shuts the open nozzle plate. After being paused for even several days, it is instantly ready to print again.
View ProductZebra ZT510 Industrial Printer
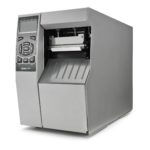
ZEBRA ZT510 – NEXT-GENERATION PRINTING THAT IS BUDGET-FRIENDLY
Designed to strike the ideal balance between performance and value, the Zebra ZT510 includes the core features you need in an industrial printer at a cost-effective price point.
View Product