Tamper Evident
Compact label dispenser for protection against manipulation of pharmaceutical packaging.
The EU Directive 2011/62/EU promulgated in 2011 introduced legal framework requirements for a pan-European safety system for prevention of counterfeit medicines. A central component, which is also addressed in the pharmaceutical law, is a clear and secure marking system for database-backed traceability and tamper-proof sealing of all packaging. Bluhm System can offer a compact, efficient and reliable solution to this requirement. A compact labelling unit is integrated into existing data matrix stations or weighing systems. Self-adhesive label seals are applied on both sides of the flap openings of pharmaceutical packing. Perforation on the labels will expose manipulation by destruction of the labels. Depending on the packaging plant, labels are either dispensed after weighing or after an inkjet printer – e.g. the Markoprint series – has printed a sequential datamatrix code onto each package.
Following this, code and seal checking by a camera system is recommended. The package will be rejected if the marking is wrong or if a seal is applied incorrectly. Only OK products will leave the plant.
Special Features
- Sealing labelling for protection against counterfeits
- Two-sided corner labelling of folding boxes
- Highly compact design to allow integration into existing plant
- Output clocking up to 300 items per minute
- Stepper motor driven applicator
- Short set-up times when switching to other product formats
- Processing of transparent, perforated labels
- Speed-independent labelling via Tamp-Wipe-On method
- Dual label roll unwinding
Adobe Reader is required to open and view PDF files. This can be downloaded free from adobe.com.
Available Documents
Tamper Evident WeberPLUSMARK – Premium Wax
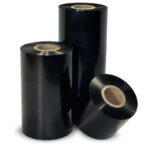
PLUSMARK is the high performance wax ribbon from Weber. It offers all
the benefits of a general purpose wax ribbon with an improved print durability
and a capability to print on synthetic label materials.
Markoprint ZTV HP
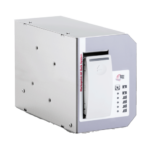
The Markoprint ZTV HP is a Central Ink Supply (CIS) system stores up to 400ml of ink for Markoprint HP Class inkjet printing systems such as the Markoprint integra One, Markoprint X2JET / X4JET, and Markoprint integra Quadro.
The large ink tank prevents frequent cartridge replacements from lowering your Overall Equipment Effectiveness (OEE). It can hold up to four single HP cartridges repaying you rapidly thanks to reduced ink prices. For non-interrupted production, the system can be paired with our NonStopPrinting printhead. Using an interface directly on the cartridge, current ink filling levels are monitored in real time. When the levels in the bulk tank fall below a certain threshold, a valve to the bulk tank opens and automatically refills it.
View ProductGeset 111 Top Labelling System
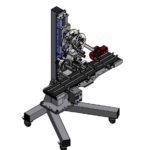
The Geset 111 labelling system is used to label square products on the top side automatically. Depending on the type and dimension of the product, different label sizes are used. The products are fed manually or by a conveying system provided by the customer at an infeed passage on the labelling system. Care should be taken on accurate alignment of the products. It is essential that the products are forwarded separately to the applicator with a gap between each other.
When the barrier is reached, an application trigger is tripped. The label applicator applies a label on the product in Wipe On procedure. The label on the top side is pushed on to the product by a brush or roller. After labelling, the products move on and can be removed from the conveyor by the customer.
View ProductMarkoprint Integra Ultimate
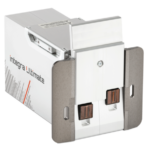
The innovative Integra Ultimate thermal inkjet printer not only provides IP65 protection against dust and moisture, but it also closes and cleans the nozzle plate at each pause. This system ensures that the printing is always clean, with faultless results even after extended breaks. As a result, the ink cartridges’ open times are multiplied many times. Two HP Class thermal inkjet ink cartridges can be used with the print head. As a result, the system produces beautiful prints with a maximum height of 25 mm.
View Product