Funai (Lexmark)
Funai (Lexmark) enables high resolution marking on any surface at very high speed.
Click on the Direct Sales Button, and contact us today to order your Funai (Lexmark) inkjet thermal inks.
- very high reliability under operational conditions
the cartridge and the complete printhead are exchanged simultaneously. This also guarantees consistent typeface quality.
- intelligent ink cartridge for increased coding reliability
ink type, manufacturer and ink content can be stored with the cartridge. The printer can therefore automatically be set to recognize the correct ink and other ink can be detected and blocked
Ink filling level detection guarantees timely detection of imminent cartridge replacement, assuring ongoing operation.
- very high printing speeds in barcode quality
up to 240 m/minute at 300 dpi (maximum 400 m/minute) with Dual Channel. There are two of every nozzle.
- extremely brilliant print image up to 900 dpi
using ink cartridges and thermo inkjets of consistent quality, achieved by ejecting tiny droplets from hundreds of minute nozzles at very high frequency and highly accurately positioned
- simple operation
the cartridges are clean and easy to handle. No special training or maintenance required.
- unique flexibility
by using several Funai printheads, max. printing heights of 12.7 to 100 mm are achieved, as well as freely configurable layouts.
- Multi-sided printing of packaging is possible
from top, bottom or side or also at different production lines.
- distances of up to 10 mm from printhead to product surface. This also enables flexible printing on convex and concave surfaces.
- virtually any porous and non-porous surfaces can be marked, depending on ink type.
- highly economical
low operating costs but also high availability through simple and clean ink exchange, zero maintenance, immediate write response and uninterrupted operation.
- simple installation
by dint of very compact design, with 2 different printhead types available
Adobe Reader is required to open and view PDF files. This can be downloaded free from adobe.com.
Available Documents
Zebra ZT510 Industrial Printer
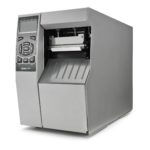
ZEBRA ZT510 – NEXT-GENERATION PRINTING THAT IS BUDGET-FRIENDLY
Designed to strike the ideal balance between performance and value, the Zebra ZT510 includes the core features you need in an industrial printer at a cost-effective price point.
View ProductMarkoprint Integra One
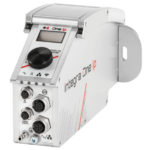
Labeling systems are not always easy to integrate into preexisting production lines. The Markoprint Integra One can be easily integrated into production processes thanks to its compact dimensions of 186 x 86 x 98 mm. The printing system has a display for data entry as well as system settings modification and verification. This information can also be viewed from mobile devices if the WLAN version is selected.
Inkjet printers should be properly protected if they are subjected to harsh manufacturing circumstances. In addition, the Markoprint integra One ip has an IP 65 protection rating. As a result, it’s ideal for use in the food industry.
View ProductPLUSMARK – Premium Wax
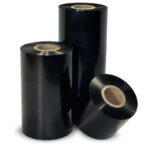
PLUSMARK is the high performance wax ribbon from Weber. It offers all
the benefits of a general purpose wax ribbon with an improved print durability
and a capability to print on synthetic label materials.
Markoprint Integra Quadro/Quadro²
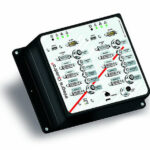
The new Markoprint Integra Quadro/Quadro² print controller can control up to four inkjet printers or four print positions at the same time. This allows you to print on both sides of primary and secondary packaging on one or two separate production lines. There are also two separate printing methods that can be used in this process.
The Markoprint Integra Quadro/Quadro² can easily cope with limited space thanks to its slender design. Installation inside or directly at the industrial line is straightforward thanks to the different fixation options. It was designed specifically for installation in control panels and machinery.
View Product