Zebra GK420
Zebra’s GK™ Series and GT800 desktop printers combine dependable printing with fast print speeds and network manageability. With their easy-to-use design, Zebra’s advanced desktop printers enable you to improve operational efficiencies.
DEPENDABLE PERFORMANCE TO IMPROVE OPERATIONAL EFFICIENCIES
The top selling desktop printer in the world, the GK420 provides a proven design and long term dependability. Both the GK420 and GT800 printer models are a top choice for a variety of mid-volume and distributed-printing applications to reliably produce quality text, barcodes or graphics.
FLEXIBLE.
The GK420 offers USB, Parallel and Serial connectivity interfaces and easy upgrades with both the ZPL and EPL programming languages. The GT800 printer supports both 300 Metre and 74 Metre ribbon capacities — without the need to change settings for different ribbon lengths. The GK420 Healthcare printer is available in the healthcare colour palette designed specifically for sterile environments.
EASY TO USE
The intuitive design of the GT800 and the GK420 printers combines a choice of three connectivity interfaces and optional 10/100 Ethernet, co-resident EPL2 and ZPL II programming languages and Unicode to ensure quick and efficient integration. The GK420 offers direct thermal only models for simplicity and cost savings.
Adobe Reader is required to open and view PDF files. This can be downloaded free from adobe.com.
Available Documents
Zebra_G-SeriesGK 420 Datasheet
Markoprint Shutter Printhead HP
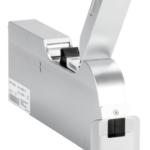
Inkjet nozzles can clog and dry up in a dusty printing environment, which is typical in wood-processing enterprises and other sectors. This results in poorly printed images. Our Markoprint Shutter Printhead HP prevents dust from entering the ink cartridge or gathering on the nozzles. During a production halt, the printhead automatically retracts the cartridge and shuts the open nozzle plate. After being paused for even several days, it is instantly ready to print again.
View ProductMarkoprint Integra Quadro/Quadro²
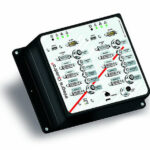
The new Markoprint Integra Quadro/Quadro² print controller can control up to four inkjet printers or four print positions at the same time. This allows you to print on both sides of primary and secondary packaging on one or two separate production lines. There are also two separate printing methods that can be used in this process.
The Markoprint Integra Quadro/Quadro² can easily cope with limited space thanks to its slender design. Installation inside or directly at the industrial line is straightforward thanks to the different fixation options. It was designed specifically for installation in control panels and machinery.
View ProductEASYMARK – Standard Wax
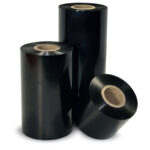
EASYMARK is the standard Weber wax ribbon which delivers consistent print
quality on any kind of paper label materials. It prints high density legible
barcodes and traceability data for short life labeling needs.
Markoprint Integra One ip LX
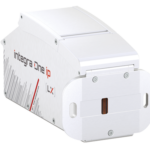
Unleash the Power of Proven Washdown Technology (IP Protection) for Seamless Performance in Complex and Demanding Applications. Experience High-Speed Printing and Effortless Operation with Up to 10 mm Print Distance. Discover Impressive Innovations, including a Patented Mechanism for Secure Ink/Printhead Unit Hold, Setting a New Standard in Printing Excellence.
View Product