Bottle-Matic II Dual Label Applicator
The Bottle-Matic II goes one step further by applying front and back pressure-sensitive labels to cylindrical objects. This makes it easy, for example, to label round containers with an eye-catching decorative label on the front and a nutrition/ingredients label on the back.
The Bottle-Matic II is available in 10″ wide and 16″ wide models that fit most products. Options include a waste re-winder that collects the label liner as it is used and a large roll adapter so you can work longer between label roll change-overs.
Bottle-Matic II Dual Label Applicators
Bottle-Matic II labellers enable you to label the front and back of all kinds of cylindrical objects by setting the desired spacing using the unit’s index knob. The operator inserts the container and depresses a footswitch and the label is applied. The machine immediately inserts a gap that was set by the index knob and applies the second label.
Most wine bottles are labelled in less than five seconds, enabling the user to quickly remove the bottle and insert another to start the procedure again. After a rhythm is established, bottles can be labelled very quickly.
Loading labels is easy as well; just feed the labels between the dispensing tables, then through the patented feed-roll assembly and snap it into place.
The Bottle-Matic comes in two sizes: Standard 10″ wide and the larger 16″ wide version for taller products. Both can handle products up to 10″ in diameter.
- Label objects from 0.5″ to 10″ diameter; ideal for test tubes to 1.5-gallon bottles.
- Gap adjustment is quick and easy.
- Accurate: Maintains repetitive gap spacing to 0.0625″ or less on most containers. Holds 0.0312″ side-to-side accuracy on most containers.
- Labels cylinders to 15″ in length (or longer if the item has a neck).
- Able to handle most tapered containers by simply adjusting the idle roller position.
- Labels over 1000 pieces per hour with average dexterity.
- Side frames are laser cut from quality steel, then formed, countersunk, deburred and inspected.
- Dispensing tables are formed out of 6061-T6 aluminium. Its peel edge is hand-milled to spec within .001″.
- Dispensing tables are polished with ultra-fine polishing compound so paper flows freely around the plate.
- Bottle-Matic II uses dual AC-shaded pole gear motors.
- Micro-switch activated; will work on all kinds of labels.
- Modifications are available for those hard-to-label containers.
Adobe Reader is required to open and view PDF files. This can be downloaded free from adobe.com.
Available Documents
bottle-maticX1Jet HP Premium MK2
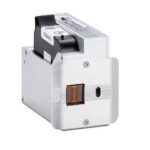
The innovative Markoprint X1JET HP inkjet printer codes absorbent and semi-absorbent surfaces quickly, accurately and reliably. It is designed for a different range of applications in the food and beverage industry as well as the chemical and pharmaceutical industry. The controller and printer are combined in one single unit, making the system extremely compact.
View ProductMarkoprint Shutter Printhead HP
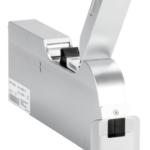
Inkjet nozzles can clog and dry up in a dusty printing environment, which is typical in wood-processing enterprises and other sectors. This results in poorly printed images. Our Markoprint Shutter Printhead HP prevents dust from entering the ink cartridge or gathering on the nozzles. During a production halt, the printhead automatically retracts the cartridge and shuts the open nozzle plate. After being paused for even several days, it is instantly ready to print again.
View ProductMarkoprint Integra PP 108
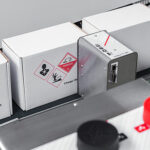
The Markoprint Integra PP108 is the first inkjet printer with SEIKO printing technology and a circulating ink system. It features a POZIFLOW circulating ink system which prevents the accumulation of air in the nozzles and ensures a permanent, clean print image without missing print due to blocked nozzles. The system’s ink tank can be installed above, below, or at the same height as the print head without any problems. The new SEIKO printhead has a print height of 108 mm and achieves a remarkable speed of up to 150 meters per minute with a high resolution of 360 dpi.
Suited to Dual Colour Printing Applications such as Hazard Labelling, Dual Colour overprinting and Direct Printing Applications to corrugate, and web printing applications, the PP108 is the latest high end, economical Inkjet System using the latest Drop on Demand Printing Technology.
View ProductGeset 111 Top Labelling System
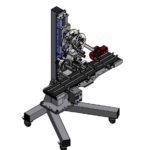
The Geset 111 labelling system is used to label square products on the top side automatically. Depending on the type and dimension of the product, different label sizes are used. The products are fed manually or by a conveying system provided by the customer at an infeed passage on the labelling system. Care should be taken on accurate alignment of the products. It is essential that the products are forwarded separately to the applicator with a gap between each other.
When the barrier is reached, an application trigger is tripped. The label applicator applies a label on the product in Wipe On procedure. The label on the top side is pushed on to the product by a brush or roller. After labelling, the products move on and can be removed from the conveyor by the customer.
View Product