Model 5300 Series Tamp-Blow Pallet Label Printer-Applicator
Weber pallet load label printer-applicators combine high print quality with simultaneous single pallet label application for the identification of unitised products prior to shipping or storage.
- Choose from a wide range of 203, 300 and 600 dpi print engines
- Capable of handling print speeds up to 16 ips
- Numerous I/O’s ease interfacing with external devices
- You can monitor its operation via a web browser
- Available with optional RFID capability
- A great way to add a labeller after your palletiser system
Model 5300 Series Tamp-Blow Pallet Label Printer-Applicator
Specially engineered for the labelling of pallet loads, each system integrates a thermal/thermal-transfer label printer and a patented tamp-blow applicator. The print-apply unit is mounted onto a heavy-duty stand which is adjustable to accommodate pallet loads of various heights. You can add this labeller to the end of your palletiser system’s conveyor.
As a pressure-sensitive label is printed, it is automatically peeled from its liner and retained by vacuum on the applicator pad. When a pallet load is delivered to the system, a product sensor initiates the extension of the tamp arm and the label is blown onto the load from approximately 0.25″.
These systems are available with high-quality print engines manufactured by Datamax, Sato and Zebra. Pallet label sizes range from a minimum of 0.75″ wide and 0.5″ long to a maximum of 7.0″ wide and 8.0″ long. The printers are capable of producing labels with variable-sized text, high-density bar codes and graphic images at print speeds up to 16 ips.
Special Features & Options
The Model 5300 pallet load system includes a number of noteworthy features that add to the operational versatility of this printer-applicator:
• Browser-based monitoring: The status of all operational functions and configurations can be monitored by logging on to a web page that is unique to each Model 5300 unit.
• Numerous I/O’s: The system can be interfaced with many types of external devices.
• One-to-one media consumption: Special label unwind and rewind dimensions are matched to the system’s ribbon supply to ensure they are consumed at the same rate, reducing downtime and eliminating partial changeovers.
• Print job storage: Multiple label printing formats can be stored in the system’s memory, making it easier for an operator to select a job directly from the applicator instead of downloading a computer file.
This system boasts numerous additional features including a microprocessor controller with downloadable firewall capability, various inputs/outputs plus durable construction that will withstand harsh industrial environments.
Other options include a 15-foot umbilical connection that enables the remote location of the unit’s controller, an adjustable stand for optimum system orientation; label-on-pad sensor for added functionality plus beacon light alerts to signal the status of label and ribbon supplies.
Adobe Reader is required to open and view PDF files. This can be downloaded free from adobe.com.
Available Documents
5300Zebra ZT510 Industrial Printer
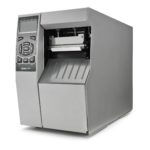
ZEBRA ZT510 – NEXT-GENERATION PRINTING THAT IS BUDGET-FRIENDLY
Designed to strike the ideal balance between performance and value, the Zebra ZT510 includes the core features you need in an industrial printer at a cost-effective price point.
View ProductZebra FS10 Fixed Industrial Scanner
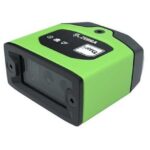
A Quick & Compact Scanning Solution
The increasing demands on international commerce and its global supply chain are pressurising businesses to deliver more and deliver faster. From manufacturing to logistics to the end customer, success is driven by the ability to move quickly and track the products that drive your business.
Now you can address it all with the compact Zebra FS10 Fixed Industrial Scanner. With a slim profile, the FS10 fits easily everywhere you need scanning. Just plug the FS10 into the USB port of a workstation, laptop, tablet or any other host device to dependably capture barcode data, from assembly to storage and fulfilment.
View ProductGeset 125 Horizontal Labelling System
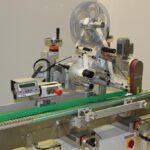
The Geset 125 labelling system is used to label cylindrical products automatically. Depending on the type and dimension of the product, different label sizes are used. The products are fed manually or by a conveying system provided by the customer at an infeed passage of the labelling system. Care should be taken on accurate alignment of the products between the two freely mounted rollers of the roll conveyor. The side guide’s position the products flush with the outside edge of the roll conveyor.
The roll conveyor feeds the products to the labeller. There the label is applied with the part running forward onto the product and it is pushed by rotation and the back pressure of the wrapping unit onto the product. The back pressure of the wrapping unit (the speed of the wrapping unit is twice as fast as the speed of the base conveyor) enables the product in rotation. The roll conveyor forwards the finished labelled products to the outfeed. Here the products are removed manually or by the customer’s conveying system.
View ProductMarkoprint NonStop Printing
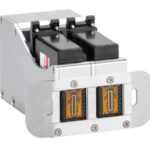
To enable continuous marking in ongoing production, our Markoprint NonStopPrinting printhead holds two alternately printing cartridges. Because the other ink cartridge is printing on the same position, each ink cartridge can be changed, cleaned, or serviced without pausing the machine.
An intelligent automatism prevents both cartridges from going empty at the same time. The first cartridge will always print two consecutive print jobs, taking turns with the second cartridge, which will only print one. This sophisticated automatism avoids both cartridges from running out at the same time. This will keep the ink from drying out in both cartridges. When the cartridge with the larger print volumes is empty, a warning will show, and the other cartridge will continue printing until it is replaced. The new cartridge will print the lower quantities to allow for you to replace the “older” cartridge. A sophisticated workflow that will boost your efficiency and productivity.
View Product