Zebra ZT200 series Printers
Zebra incorporated extensive customer feedback, as well as the legacy of its Stripe® and S4M™ printers, to create the new ZT200 series printers, which feature elegant space-saving design, effortless setup, intuitive user operation, and ease of service and maintenance. Whether you are adopting barcode technology for the first time or upgrading existing printer models, the ZT200 series is the right choice for a variety of labelling applications. These innovative new printers provide many user benefits.
The ZT200 series offers a streamlined design and smaller footprint that takes up less physical space than the Stripe and S4M models. ZT200 series printers require minimal operator training and benefit from tool-less standard component maintenance and a durable design to minimise service. Your IT staff will appreciate the backwards compatibility, since it allows for new printers to be up and running with minimal downtime.
The ZT200 series uses Zebra’s Link-OS™ environment: an open platform that pairs an operating system for smart Zebra devices with powerful software apps. AirWatch® Connector allows for simplified device management.The Print Station app quickly enables tablet- and smartphone-based printing. And with Cloud Connect, the ZT200 series printer can connect to the cloud directly and securely.
The ZT200 series has been designed for ease of use, versatility and outstanding value.
Adobe Reader is required to open and view PDF files. This can be downloaded free from adobe.com.
Available Documents
Zebra® ZT200™ seriesGeset 111 Top Labelling System
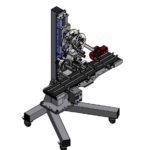
The Geset 111 labelling system is used to label square products on the top side automatically. Depending on the type and dimension of the product, different label sizes are used. The products are fed manually or by a conveying system provided by the customer at an infeed passage on the labelling system. Care should be taken on accurate alignment of the products. It is essential that the products are forwarded separately to the applicator with a gap between each other.
When the barrier is reached, an application trigger is tripped. The label applicator applies a label on the product in Wipe On procedure. The label on the top side is pushed on to the product by a brush or roller. After labelling, the products move on and can be removed from the conveyor by the customer.
View ProductMarkoprint Integra PP 108
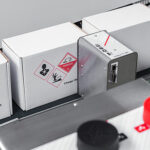
The Markoprint Integra PP108 is the first inkjet printer with SEIKO printing technology and a circulating ink system. It features a POZIFLOW circulating ink system which prevents the accumulation of air in the nozzles and ensures a permanent, clean print image without missing print due to blocked nozzles. The system’s ink tank can be installed above, below, or at the same height as the print head without any problems. The new SEIKO printhead has a print height of 108 mm and achieves a remarkable speed of up to 150 meters per minute with a high resolution of 360 dpi.
Suited to Dual Colour Printing Applications such as Hazard Labelling, Dual Colour overprinting and Direct Printing Applications to corrugate, and web printing applications, the PP108 is the latest high end, economical Inkjet System using the latest Drop on Demand Printing Technology.
View ProductGeset 125 Horizontal Labelling System
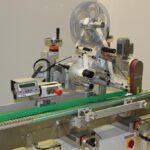
The Geset 125 labelling system is used to label cylindrical products automatically. Depending on the type and dimension of the product, different label sizes are used. The products are fed manually or by a conveying system provided by the customer at an infeed passage of the labelling system. Care should be taken on accurate alignment of the products between the two freely mounted rollers of the roll conveyor. The side guide’s position the products flush with the outside edge of the roll conveyor.
The roll conveyor feeds the products to the labeller. There the label is applied with the part running forward onto the product and it is pushed by rotation and the back pressure of the wrapping unit onto the product. The back pressure of the wrapping unit (the speed of the wrapping unit is twice as fast as the speed of the base conveyor) enables the product in rotation. The roll conveyor forwards the finished labelled products to the outfeed. Here the products are removed manually or by the customer’s conveying system.
View ProductULTRAPRINT – High durability resin
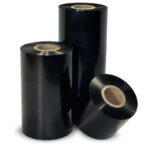
ULTRAPLATE is the standard resin ribbon from Weber. It is dedicated to
applications requiring a perfect printing quality and excellent mechanical
resistances. Its high versatility (it also prints on coated papers) and its
performances (sharpness, printing speed) have resulted in making
ULTRAPLATE a market reference.