Legi-Air 4050E Precision Labelling
E is a synonym for the word “ENHANCED”. Based on a modular construction the LA 4050E is capable of numerous methods to print and apply a label. The design comprises a feeder module, a printing module, label winder and unwinder with numerous applicator types. The standard Tamp-Blow system has a quick-change system for changing the tamp pad which significantly reduces the changeover time to other label formats.
LA 4050E Modular for Cutomisation
The Legi-Air 4050E prints and feeds labels in lengths of 10 x 5 mm up to 180 x 300 mm with a feeder output of up to 210 labels per minute with the blow-box method. To optimise logistics in particular.
A two-stage vacuum for label transportation and feeding facilitates flexible adaptation to the labelling material and guarantees process reliability during labelling. Thanks to electronic vacuum and pressure measurement in conjunction with Festo pneumatics, the Legi-Air 4050 E feeds labels with maximum precision and speed.
Swivel applicators are available which allow for label application in numerous locations . A removable display controller supports this flexibility and facilitates simple and quick operation by means of targeted plain text user information and stored system parameters. Flexible control or networking of systems guarantees conventional standards such as Ethernet, serial and parallel data connections as well as USB.
Print Engine Technology
Working closely with all major international print engine manufacturers Weber has designed the LA 4050E with flexibility and localization in mind. Whether Zebra, Sato, Avery, CAB or Datamax-O’Neil is the print engine of the choice, the LA 4050E can accommodate. Where no customer preference is indicated our fully trained, experience and certified Sales staff will recommend the best print engine and application method to suit your individual requirements.
The LA 4050E also can be equipped with an RFID print module that supports existing RFID standards.
Adobe Reader is required to open and view PDF files. This can be downloaded free from adobe.com.
Available Documents
LA4050E_ukMarkoprint IP-Jet
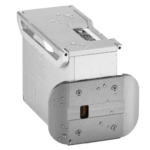
The thermal inkjet printer IP-JET HP MK3 has been specifically designed for usage in dusty or damp situations. It is especially ideal for the food sector, as well as the plastics, pharmaceutical, and chemical industries, due to its IP65 protection level.
The IP-JET HP is a small inkjet printer with a printhead and control unit housed in one unit. Water and dust are kept out of the cartridge by sealing it and pressurizing it. The power supply features a waterproof connector, and the external connections’ connectors are secured with an IP67 rating. The printhead does not need to be covered or removed for wet cleaning, unlike many other printers on the market.
View ProductMarkoprint Integra PP 108
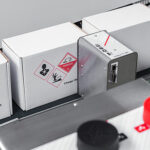
The Markoprint Integra PP108 is the first inkjet printer with SEIKO printing technology and a circulating ink system. It features a POZIFLOW circulating ink system which prevents the accumulation of air in the nozzles and ensures a permanent, clean print image without missing print due to blocked nozzles. The system’s ink tank can be installed above, below, or at the same height as the print head without any problems. The new SEIKO printhead has a print height of 108 mm and achieves a remarkable speed of up to 150 meters per minute with a high resolution of 360 dpi.
Suited to Dual Colour Printing Applications such as Hazard Labelling, Dual Colour overprinting and Direct Printing Applications to corrugate, and web printing applications, the PP108 is the latest high end, economical Inkjet System using the latest Drop on Demand Printing Technology.
View ProductPLUSMARK – Premium Wax
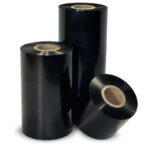
PLUSMARK is the high performance wax ribbon from Weber. It offers all
the benefits of a general purpose wax ribbon with an improved print durability
and a capability to print on synthetic label materials.
X1Jet HP Premium MK2
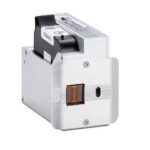
The innovative Markoprint X1JET HP inkjet printer codes absorbent and semi-absorbent surfaces quickly, accurately and reliably. It is designed for a different range of applications in the food and beverage industry as well as the chemical and pharmaceutical industry. The controller and printer are combined in one single unit, making the system extremely compact.
View Product