Legi-air 6000
High performance label printing dispenser for labelling shipping cartons.
The modular concept of the Legi-air label Print apply system allows the unit to be customised to suit existing production lines.
Legi-air 6000
Product traceability, quality assurance, tracking and tracing in logistics or individual identification of products for just-in- time production – these are just some of the current industry demands that are catered for with this system. Interchangeable dispensing heads allow the use of different label sizes. Print engines by leading global manufacturers such as Zebra, Datamax, CaB etc allows an optimal match to the application and its specific printing requirements. Reaching 400 products per hour, the Legi-air 6000 high performance printing and application system will label passing cartons of varying height quickly and efficiently.
Differences in product height of up to 500 mm can be achieved thanks to the high performance stroke unit. these peak performances are achieved using a servo motor driven dispensing applicator and carbon fibre construction.
Once the sensor has initially determined the height of the approaching product for labelling, the applicator will move to the correct position at high speed. this reduces the travelling distance for labelling and the Legi-air 6000 will simultaneously label more accurately and up to 50 percent faster than a printing dispenser with a pneumatically driven cylinder.
The new redesigned microprocessor controller is optimal in terms of both cost and space. This makes the system highly compact and facilitates easy integration into existing operating environments. The Legi-air 6000 will handle large label rolls with an ergonomically adjustable reel holder taking maximum roll size of up to 350 mm diameter. This results in higher efficiency production runs and less downtime for Label Reel Change.
The intelligent construction allows easy access to system components for servicing and or maintenance, enabling convenient changing of labels and foils as well as particularly easy cleaning of the print module’s thermal print head, as needed.
Adobe Reader is required to open and view PDF files. This can be downloaded free from adobe.com.
Available Documents
Legi-Air_6000 leafletGeset 125 Horizontal Labelling System
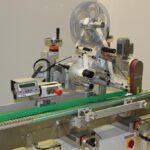
The Geset 125 labelling system is used to label cylindrical products automatically. Depending on the type and dimension of the product, different label sizes are used. The products are fed manually or by a conveying system provided by the customer at an infeed passage of the labelling system. Care should be taken on accurate alignment of the products between the two freely mounted rollers of the roll conveyor. The side guide’s position the products flush with the outside edge of the roll conveyor.
The roll conveyor feeds the products to the labeller. There the label is applied with the part running forward onto the product and it is pushed by rotation and the back pressure of the wrapping unit onto the product. The back pressure of the wrapping unit (the speed of the wrapping unit is twice as fast as the speed of the base conveyor) enables the product in rotation. The roll conveyor forwards the finished labelled products to the outfeed. Here the products are removed manually or by the customer’s conveying system.
View ProductMarkoprint Shutter Printhead HP
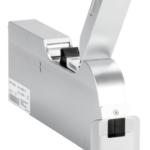
Inkjet nozzles can clog and dry up in a dusty printing environment, which is typical in wood-processing enterprises and other sectors. This results in poorly printed images. Our Markoprint Shutter Printhead HP prevents dust from entering the ink cartridge or gathering on the nozzles. During a production halt, the printhead automatically retracts the cartridge and shuts the open nozzle plate. After being paused for even several days, it is instantly ready to print again.
View ProductZebra FS40 Fixed Industrial Scanner

Enable Performance. Inspire Potential. Experience The Difference.
Today more than ever, the increasing demands of international commerce and its global supply chain are pressuring companies to deliver more — and to do it faster. From manufacturing to logistics to the end customer, success is driven by the ability to quickly move and track the products that drive your business.
Address it all with Zebra’s FS40 Fixed Industrial Scanner designed to meet the comprehensive requirements of today’s production and delivery processes. The FS40 easily keeps pace with the fastest moving operations, enabling track-and-trace through the automatic and flawless decode of information on every part and package as it moves through production, storage and fulfilment — capturing even the most challenging barcodes. The result? Best-in-class production, warehousing, distribution and logistics processes that inspire businesses to reach their highest potential.
View ProductZebra ZT510 Industrial Printer
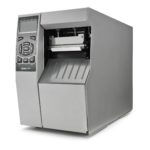
ZEBRA ZT510 – NEXT-GENERATION PRINTING THAT IS BUDGET-FRIENDLY
Designed to strike the ideal balance between performance and value, the Zebra ZT510 includes the core features you need in an industrial printer at a cost-effective price point.
View Product