Laser Applicator: Alpha-Laser Label Applicator
The laser labeling solution comprises an Alpha label dispenser and a Solaris CO2 laser. The Alpha-Laser writes variable additional information such as best before dates, graphics or logistics data on pre-printed labels immediately before application.
Cost-effective and reliable labeling
The compact Alpha-Laser labels reliably and cost-effectively especially where large batches are processed and must be traced. This technology is ideally suited especially for harsh environments since the laser, as the printing unit, is considered virtually non-wearing compared to conventional printing methods.
The laser has a significantly longer service life by comparison and guarantees significantly higher availability, with no consumables or pressure bars. It ensures uninterrupted production. The laser writes all information – also batch and lot numbers – on any part of the label, with or across the direction of travel. The laser can write in black on laser-activable labels with a special finishing coat. No decomposition products are created and the labels are not damaged. The print is smear- and scratch-resistant.
The advantages of the Alpha-Laser in a nutshell:
- Any type of label made of paper or foil or foil-laminated material can be used
- Printing on a coating that can be activated exclusively by laser
- Printing of information in pre-printed color fields
- Writes codes and graphics
- No consumables
- Low maintenance
- Smear- and scratch-proof marking
- High marking speeds
- High process reliability and low running costs.
Adobe Reader is required to open and view PDF files. This can be downloaded free from adobe.com.
Available Documents
24300Markoprint Integra One ip LX
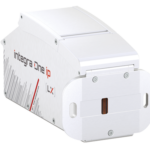
Unleash the Power of Proven Washdown Technology (IP Protection) for Seamless Performance in Complex and Demanding Applications. Experience High-Speed Printing and Effortless Operation with Up to 10 mm Print Distance. Discover Impressive Innovations, including a Patented Mechanism for Secure Ink/Printhead Unit Hold, Setting a New Standard in Printing Excellence.
View ProductMarkoprint Integra PP 108
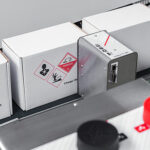
The Markoprint Integra PP108 is the first inkjet printer with SEIKO printing technology and a circulating ink system. It features a POZIFLOW circulating ink system which prevents the accumulation of air in the nozzles and ensures a permanent, clean print image without missing print due to blocked nozzles. The system’s ink tank can be installed above, below, or at the same height as the print head without any problems. The new SEIKO printhead has a print height of 108 mm and achieves a remarkable speed of up to 150 meters per minute with a high resolution of 360 dpi.
Suited to Dual Colour Printing Applications such as Hazard Labelling, Dual Colour overprinting and Direct Printing Applications to corrugate, and web printing applications, the PP108 is the latest high end, economical Inkjet System using the latest Drop on Demand Printing Technology.
View ProductZebra FS40 Fixed Industrial Scanner

Enable Performance. Inspire Potential. Experience The Difference.
Today more than ever, the increasing demands of international commerce and its global supply chain are pressuring companies to deliver more — and to do it faster. From manufacturing to logistics to the end customer, success is driven by the ability to quickly move and track the products that drive your business.
Address it all with Zebra’s FS40 Fixed Industrial Scanner designed to meet the comprehensive requirements of today’s production and delivery processes. The FS40 easily keeps pace with the fastest moving operations, enabling track-and-trace through the automatic and flawless decode of information on every part and package as it moves through production, storage and fulfilment — capturing even the most challenging barcodes. The result? Best-in-class production, warehousing, distribution and logistics processes that inspire businesses to reach their highest potential.
View ProductMarkoprint ZTV HP
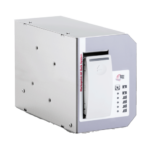
The Markoprint ZTV HP is a Central Ink Supply (CIS) system stores up to 400ml of ink for Markoprint HP Class inkjet printing systems such as the Markoprint integra One, Markoprint X2JET / X4JET, and Markoprint integra Quadro.
The large ink tank prevents frequent cartridge replacements from lowering your Overall Equipment Effectiveness (OEE). It can hold up to four single HP cartridges repaying you rapidly thanks to reduced ink prices. For non-interrupted production, the system can be paired with our NonStopPrinting printhead. Using an interface directly on the cartridge, current ink filling levels are monitored in real time. When the levels in the bulk tank fall below a certain threshold, a valve to the bulk tank opens and automatically refills it.
View Product