Portable Print & Ship
The Barcode Reader – efficiency in the form of a device
The “Portable Print & Ship” solution utilises a new kind of small handheld reader. The device can scan barcodes and it also contains a read/write unit for tags.
Barcode content is automatically converted into an EPC (Electronic Product Code) and the data is immediately written to a tag, without a printing unit being required. “Handy Tags” ensure the process is both rapid and uncomplicated. In order to ensure satisfactory performance in later processing, even when using on metal surfaces and products containing liquids, “Handy Flag Tags” are available, equipped with a special backing paper. No additional equipment is necessary: the label can later be simply folded by hand so that the portion containing the RFID tag is raised slightly above the surface. This significantly improves the read performance.
Easy transmission of product details
The innovative RFID technology facilitates the process of identifying products and acquires all the necessary information regarding the different products. Even with difficult ‘external’ conditions including metallic surfaces, the chip-based system allows for an easy transmission of product details. The ‘main piece’ of this technology consists of a transponder – a chip which stores the data, also known as the Electronic Product Code (EPC).
This code and all the included information can then be read by barcode readers. Today these handy devices are no longer simply readers, but are now also multifunctional with the capability to write new tags. With these practical readers it is just as easy to scan barcodes and write or read tags as it is to print new ones at the same time. Here, the device makes work processes easier and improves time efficiency. In comparison to only a few years ago when everything had to be registered, counted or read manually, the new generation of readers, together with technologies like RFID, have really made logistical processes a lot simpler.
How does it work?
The former original barcode system is being gradually complemented by this new technology. Regardless, the Weber Barcode Reader is designed and able to manage both of these systems. This device is fully equipped for both barcode reading and the new RFID technology.
When the barcode is read it directly transforms this information into an EPC. If required, the obtained data can then be instantly printed onto a tag. The practical Barcode Reader substitutes an additional printer when tags are needed immediately. Just one device combines all functions which are necessary for efficient work processes in logistical and similar businesses, even though a professional bar code label printer is typically recommended for the general printing of labels and tags.
Special features of the barcode reader
In addition to the already mentioned functions of the reader, there is a feature which can be used to manage more ‘extreme’ cases. ‘Handy Tags’ ensure that a smooth workflow is guaranteed in all circumstances. Products containing liquids or with metal surfaces are sometimes difficult to deal with in terms of reading their information or writing a useful tag for them. Such difficulties can be eased by using the ‘Handy Flag Tags’ – tags made from a special paper.
This label or tag can also be made bolder allowing for improved legibility. Due to the special bolding, a little distance is created between the product surface and the part of the tag which includes the RFID-encoded information. The information can then be read without being negatively affected by the surface. With the barcode reader no other devices or equipment are necessary – it is all included in one reader.
Adobe Reader is required to open and view PDF files. This can be downloaded free from adobe.com.
Available Documents
Markoprint NonStop Printing
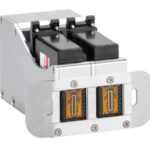
To enable continuous marking in ongoing production, our Markoprint NonStopPrinting printhead holds two alternately printing cartridges. Because the other ink cartridge is printing on the same position, each ink cartridge can be changed, cleaned, or serviced without pausing the machine.
An intelligent automatism prevents both cartridges from going empty at the same time. The first cartridge will always print two consecutive print jobs, taking turns with the second cartridge, which will only print one. This sophisticated automatism avoids both cartridges from running out at the same time. This will keep the ink from drying out in both cartridges. When the cartridge with the larger print volumes is empty, a warning will show, and the other cartridge will continue printing until it is replaced. The new cartridge will print the lower quantities to allow for you to replace the “older” cartridge. A sophisticated workflow that will boost your efficiency and productivity.
View ProductGeset 117 Top and Bottom Labelling System
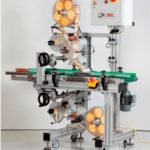
The Geset 117 labelling system is used to label square products on the top and bottom side automatically. Depending on the type and dimension of the product, different label sizes are used. The products are fed manually or by a conveying system provided by the customer at an infeed passage on the labelling system. Care should be taken on accurate alignment of the products. It is essential that the products are forwarded separately to the applicator with a gap between each other.
When the light barrier is reached, an application trigger is tripped. Both label applicators apply then in Wipe On procedure a label onto the product. The label on top side is pushed on the product by a brush or roller. The label on bottom side is pushed on the product by the self-weight of the product. After labelling the products move on and can be removed from conveyor by the customer.
View ProductMarkoprint Integra PP 108
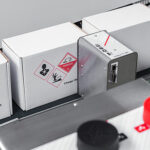
The Markoprint Integra PP108 is the first inkjet printer with SEIKO printing technology and a circulating ink system. It features a POZIFLOW circulating ink system which prevents the accumulation of air in the nozzles and ensures a permanent, clean print image without missing print due to blocked nozzles. The system’s ink tank can be installed above, below, or at the same height as the print head without any problems. The new SEIKO printhead has a print height of 108 mm and achieves a remarkable speed of up to 150 meters per minute with a high resolution of 360 dpi.
Suited to Dual Colour Printing Applications such as Hazard Labelling, Dual Colour overprinting and Direct Printing Applications to corrugate, and web printing applications, the PP108 is the latest high end, economical Inkjet System using the latest Drop on Demand Printing Technology.
View ProductGeset 111 Top Labelling System
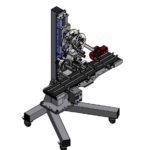
The Geset 111 labelling system is used to label square products on the top side automatically. Depending on the type and dimension of the product, different label sizes are used. The products are fed manually or by a conveying system provided by the customer at an infeed passage on the labelling system. Care should be taken on accurate alignment of the products. It is essential that the products are forwarded separately to the applicator with a gap between each other.
When the barrier is reached, an application trigger is tripped. The label applicator applies a label on the product in Wipe On procedure. The label on the top side is pushed on to the product by a brush or roller. After labelling, the products move on and can be removed from the conveyor by the customer.
View Product