Portable Print & Ship
The Barcode Reader – efficiency in the form of a device
The “Portable Print & Ship” solution utilises a new kind of small handheld reader. The device can scan barcodes and it also contains a read/write unit for tags.
Barcode content is automatically converted into an EPC (Electronic Product Code) and the data is immediately written to a tag, without a printing unit being required. “Handy Tags” ensure the process is both rapid and uncomplicated. In order to ensure satisfactory performance in later processing, even when using on metal surfaces and products containing liquids, “Handy Flag Tags” are available, equipped with a special backing paper. No additional equipment is necessary: the label can later be simply folded by hand so that the portion containing the RFID tag is raised slightly above the surface. This significantly improves the read performance.
Easy transmission of product details
The innovative RFID technology facilitates the process of identifying products and acquires all the necessary information regarding the different products. Even with difficult ‘external’ conditions including metallic surfaces, the chip-based system allows for an easy transmission of product details. The ‘main piece’ of this technology consists of a transponder – a chip which stores the data, also known as the Electronic Product Code (EPC).
This code and all the included information can then be read by barcode readers. Today these handy devices are no longer simply readers, but are now also multifunctional with the capability to write new tags. With these practical readers it is just as easy to scan barcodes and write or read tags as it is to print new ones at the same time. Here, the device makes work processes easier and improves time efficiency. In comparison to only a few years ago when everything had to be registered, counted or read manually, the new generation of readers, together with technologies like RFID, have really made logistical processes a lot simpler.
How does it work?
The former original barcode system is being gradually complemented by this new technology. Regardless, the Weber Barcode Reader is designed and able to manage both of these systems. This device is fully equipped for both barcode reading and the new RFID technology.
When the barcode is read it directly transforms this information into an EPC. If required, the obtained data can then be instantly printed onto a tag. The practical Barcode Reader substitutes an additional printer when tags are needed immediately. Just one device combines all functions which are necessary for efficient work processes in logistical and similar businesses, even though a professional bar code label printer is typically recommended for the general printing of labels and tags.
Special features of the barcode reader
In addition to the already mentioned functions of the reader, there is a feature which can be used to manage more ‘extreme’ cases. ‘Handy Tags’ ensure that a smooth workflow is guaranteed in all circumstances. Products containing liquids or with metal surfaces are sometimes difficult to deal with in terms of reading their information or writing a useful tag for them. Such difficulties can be eased by using the ‘Handy Flag Tags’ – tags made from a special paper.
This label or tag can also be made bolder allowing for improved legibility. Due to the special bolding, a little distance is created between the product surface and the part of the tag which includes the RFID-encoded information. The information can then be read without being negatively affected by the surface. With the barcode reader no other devices or equipment are necessary – it is all included in one reader.
Adobe Reader is required to open and view PDF files. This can be downloaded free from adobe.com.
Available Documents
Markoprint Integra Ultimate
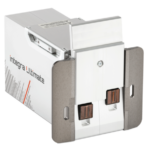
The innovative Integra Ultimate thermal inkjet printer not only provides IP65 protection against dust and moisture, but it also closes and cleans the nozzle plate at each pause. This system ensures that the printing is always clean, with faultless results even after extended breaks. As a result, the ink cartridges’ open times are multiplied many times. Two HP Class thermal inkjet ink cartridges can be used with the print head. As a result, the system produces beautiful prints with a maximum height of 25 mm.
View ProductMarkoprint NonStop Printing
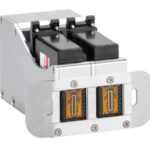
To enable continuous marking in ongoing production, our Markoprint NonStopPrinting printhead holds two alternately printing cartridges. Because the other ink cartridge is printing on the same position, each ink cartridge can be changed, cleaned, or serviced without pausing the machine.
An intelligent automatism prevents both cartridges from going empty at the same time. The first cartridge will always print two consecutive print jobs, taking turns with the second cartridge, which will only print one. This sophisticated automatism avoids both cartridges from running out at the same time. This will keep the ink from drying out in both cartridges. When the cartridge with the larger print volumes is empty, a warning will show, and the other cartridge will continue printing until it is replaced. The new cartridge will print the lower quantities to allow for you to replace the “older” cartridge. A sophisticated workflow that will boost your efficiency and productivity.
View ProductGeset 125 Horizontal Labelling System
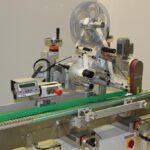
The Geset 125 labelling system is used to label cylindrical products automatically. Depending on the type and dimension of the product, different label sizes are used. The products are fed manually or by a conveying system provided by the customer at an infeed passage of the labelling system. Care should be taken on accurate alignment of the products between the two freely mounted rollers of the roll conveyor. The side guide’s position the products flush with the outside edge of the roll conveyor.
The roll conveyor feeds the products to the labeller. There the label is applied with the part running forward onto the product and it is pushed by rotation and the back pressure of the wrapping unit onto the product. The back pressure of the wrapping unit (the speed of the wrapping unit is twice as fast as the speed of the base conveyor) enables the product in rotation. The roll conveyor forwards the finished labelled products to the outfeed. Here the products are removed manually or by the customer’s conveying system.
View ProductZebra FS40 Fixed Industrial Scanner

Enable Performance. Inspire Potential. Experience The Difference.
Today more than ever, the increasing demands of international commerce and its global supply chain are pressuring companies to deliver more — and to do it faster. From manufacturing to logistics to the end customer, success is driven by the ability to quickly move and track the products that drive your business.
Address it all with Zebra’s FS40 Fixed Industrial Scanner designed to meet the comprehensive requirements of today’s production and delivery processes. The FS40 easily keeps pace with the fastest moving operations, enabling track-and-trace through the automatic and flawless decode of information on every part and package as it moves through production, storage and fulfilment — capturing even the most challenging barcodes. The result? Best-in-class production, warehousing, distribution and logistics processes that inspire businesses to reach their highest potential.
View Product