Performance Series
The Datamax-O’Neil p1120n Near Edge Performance Printer offers a unique near-edge printhead that allows full use of the label giving customers the ability to design and code barcodes that support detailed information. The flexible multimedia printing allows labels to be printed on synthetics, tags, self-adhesives and plastics. The near-edge printhead gives users the ability to integrate barcode printing across a wide variety of applications. The p1120n also offers auto-loading capabilities, a user-friendly touchscreen, and uses industry standard PCL printer language making it easy to integrate.
Like the rest of the Performance Series printers, the p1120n was designed to resolve a number of issues customers have been having with thermal printers for many years. This had resulted in a printer family that is the easiest to load, easiest to use and easiest to integrate of any thermal printers available anywhere. The inclusion of Incorporating PCL, an industry standard printer language, allows the printer to run on a variety of operating systems, so it is independent of any application software running on a computer. This ensures faster and easier plug-play integration, getting your printer systems up and running sooner.
Applications:
Manufacturing
• Asset Tracking
• Finished Goods Marking
• Agency Labels
• Case Labels
• Instruction labels
Transportation and Logistics
• Cross Docking
• Sorting Centers
• Shipping Labels
• Pallet Tracking[/one_third]
[one_third last=”yes”]
Pharmaceuticals
• Compliance Labels
• Product Identification
• Track and Trace
• Pick Lists
Horticulture
• Plant Stakes up to .025″/.635mm Thick
• Tree Wraps
• Polyester Pot Labels[/one_third]
Adobe Reader is required to open and view PDF files. This can be downloaded free from adobe.com.
Available Documents
Performance [N] SeriesMarkoprint Integra One
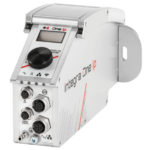
Labeling systems are not always easy to integrate into preexisting production lines. The Markoprint Integra One can be easily integrated into production processes thanks to its compact dimensions of 186 x 86 x 98 mm. The printing system has a display for data entry as well as system settings modification and verification. This information can also be viewed from mobile devices if the WLAN version is selected.
Inkjet printers should be properly protected if they are subjected to harsh manufacturing circumstances. In addition, the Markoprint integra One ip has an IP 65 protection rating. As a result, it’s ideal for use in the food industry.
View ProductMarkoprint Integra Ultimate
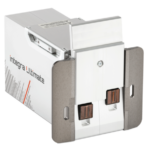
The innovative Integra Ultimate thermal inkjet printer not only provides IP65 protection against dust and moisture, but it also closes and cleans the nozzle plate at each pause. This system ensures that the printing is always clean, with faultless results even after extended breaks. As a result, the ink cartridges’ open times are multiplied many times. Two HP Class thermal inkjet ink cartridges can be used with the print head. As a result, the system produces beautiful prints with a maximum height of 25 mm.
View ProductZebra FS70 Fixed Industrial Scanner
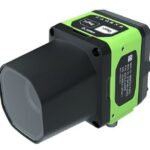
Today more than ever, the increasing demands of international commerce and its global supply chain are pressuring companies to deliver more — and to do it faster. From manufacturing to logistics to the end customer, success is driven by the ability to quickly move and track the products that drive your business.
The FS70 Fixed Industrial Scanner is your configurable and customisable solution. Easily keep pace with your business, enabling quality control and track-and-trace of every part and package as it moves through production, storage and fulfilment. Whether you need a high-powered lens to read a very small barcode from a long distance, or a wide-angle lens to capture barcodes on extremely large parts, the FS70 addresses it all. C-mount external lenses allow you to achieve the working range and field of view your application and environment requires. And compatibility with virtually any external lighting solution ensures reading of the most challenging barcodes — even low-contrast direct part marks or those printed on curved or reflective surfaces. The result? Best-in-class production, warehousing, distribution and logistics processes that inspire your business to reach its highest potential.
View Product
Markoprint Integra Quadro/Quadro²
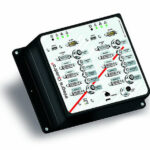
The new Markoprint Integra Quadro/Quadro² print controller can control up to four inkjet printers or four print positions at the same time. This allows you to print on both sides of primary and secondary packaging on one or two separate production lines. There are also two separate printing methods that can be used in this process.
The Markoprint Integra Quadro/Quadro² can easily cope with limited space thanks to its slender design. Installation inside or directly at the industrial line is straightforward thanks to the different fixation options. It was designed specifically for installation in control panels and machinery.
View Product